铝屑熔解炉在生产过程中会产生大量余热,对其进行回收利用不仅能降低能源消耗,还能提升生产效率。以下是铝屑熔解炉余热回收利用方案的具体内容:
- 高温炉气余热
- 铝屑熔解时炉内产生的高温烟气(温度通常为 600-1200℃),携带大量显热和潜热。
- 特点:热量占比高(约 30%-50%),温度波动大,含粉尘和少量铝蒸汽。
- 炉体散热余热
- 熔解炉炉壁、炉门等部位的辐射和对流散热(温度约 100-300℃)。
- 特点:温度较低但持续存在,散热面积大。
- 冷却系统余热
- 炉体冷却循环水、设备润滑油冷却等产生的余热(温度约 50-90℃)。
- 特点:温度低、热量分散,但稳定性高。
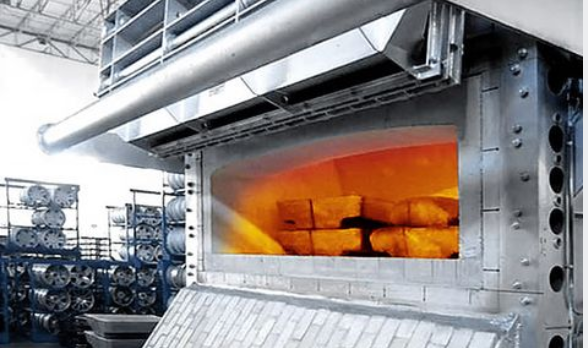
余热锅炉发电 / 产蒸汽
- 原理:通过余热锅炉将高温烟气热量传递给水,生成蒸汽用于驱动汽轮机发电或直接供热。
- 设备:管式余热锅炉、板式换热器。
- 应用场景:大型铝屑熔解炉(产能≥500 吨 / 天),适合集中供电或供热需求。
- 效益:发电效率约 15%-25%,吨铝屑可回收电能 50-100kWh。
空气 / 燃料预热
- 原理:通过热交换器(如板式、管式)用高温烟气预热助燃空气或燃料气。
- 设备:蓄热式换热器(RTO)、对流式预热器。
- 应用场景:所有规模熔解炉,可降低燃料消耗 10%-20%。
- 案例:某铝加工企业采用蓄热式燃烧系统,烟气温度从 900℃降至 200℃,燃料成本下降 18%。
粉尘协同处理
- 技术:在余热回收前设置布袋除尘器或静电除尘器,分离烟气中的铝粉尘(可回收再利用),避免换热器堵塞。
炉壁隔热改造 + 热管回收
- 措施:
- 炉壁加装纳米隔热材料(如气凝胶毡),减少散热损失(散热效率降低 30%-50%)。
- 安装热管换热器,将炉壁辐射热传递给循环水,加热至 60-80℃用于厂区生活热水或车间供暖。
- 效益:吨铝屑可回收热量约 20-30kWh,相当于节省 5-8kg 标准煤。
热泵技术回收冷却余热
- 原理:通过热泵系统将冷却循环水(50-70℃)的热量提升至 80-95℃,用于预热铝屑或生产工艺用水。
- 设备:水源热泵机组、溴化锂吸收式热泵。
- 应用场景:中等规模熔解炉,配合蓄热水箱实现稳定供热。
余热多级利用流程
蓄热储能系统
- 配置相变蓄热装置(如熔融盐、水合盐),在熔解炉低负荷时储存余热,高负荷时释放,提升系统稳定性。
- 余热回收系统集成要点
- 温度匹配:根据余热温度选择对应技术(如>500℃优先发电,300-500℃预热,<300℃供热)。
- 防腐耐磨:烟气含氯离子和铝粉尘,换热器需采用耐高温不锈钢(如 310S)或陶瓷涂层。
- 核心设备选型
设备类型 | 适用余热温度 | 效率 | 投资成本 |
---|
余热锅炉 | 600-1200℃ | 85%-92% | 高(50-200 万元) |
蓄热式换热器 | 400-800℃ | 90%-95% | 中(20-50 万元) |
热泵机组 | 50-90℃ | COP 3.0-4.0 | 中(10-30 万元) |
热管换热器 | 100-300℃ | 75%-85% | 低(5-15 万元) |
- 经济效益
- 节能收益:吨铝屑回收余热可降低综合能耗 10%-15%,按年产 1 万吨铝屑计算,年节省标煤约 1500-2000 吨,折合电费 80-120 万元。
- 投资回报:系统投资回收期通常为 2-4 年(取决于规模和技术选型)。
- 环保效益
- 减少 CO₂排放约 3000-5000 吨 / 年,降低烟气热污染,符合国家 “双碳” 政策。
- 实施建议
- 前期评估:委托能源审计机构测算余热总量、温度分布及回收潜力。
- 分步实施:优先实施高温炉气回收(效益显著),再逐步推进低品位余热利用。
- 智能监控:加装 PLC 控制系统,实时监测余热参数,优化能量分配。
- 某铝业公司:在 10 吨铝屑熔解炉配套余热锅炉 + 空气预热系统,年回收蒸汽 1.2 万吨,发电 80 万 kWh,投资回收期 3.2 年。
- 欧洲某铝加工企业:采用 “蓄热式燃烧 + 热泵” 组合技术,将余热利用率提升至 75%,吨铝能耗降至 4.2GJ(原 5.8GJ)。
通过以上方案,可实现铝屑熔解炉余热的高效回收,同时提升企业能源利用率和竞争力。实际应用中需结合生产规模、场地条件及投资预算优化技术组合。
文章源自炬鼎熔炉-江浙沪铝合金集中熔化炉厂家|中频感应熔炼炉|铝屑熔解炉报价-品牌直供·节能技术-https://www.judrl.com/3479.html文章源自炬鼎熔炉-江浙沪铝合金集中熔化炉厂家|中频感应熔炼炉|铝屑熔解炉报价-品牌直供·节能技术-https://www.judrl.com/3479.html