在电阻丝加热
铝合金熔炼炉的过程中,铝合金的温度均匀分布需要综合考虑加热方式、熔炉结构设计及热传递机制。以下从多个维度详细解析温度均匀分布的实现原理与方法:
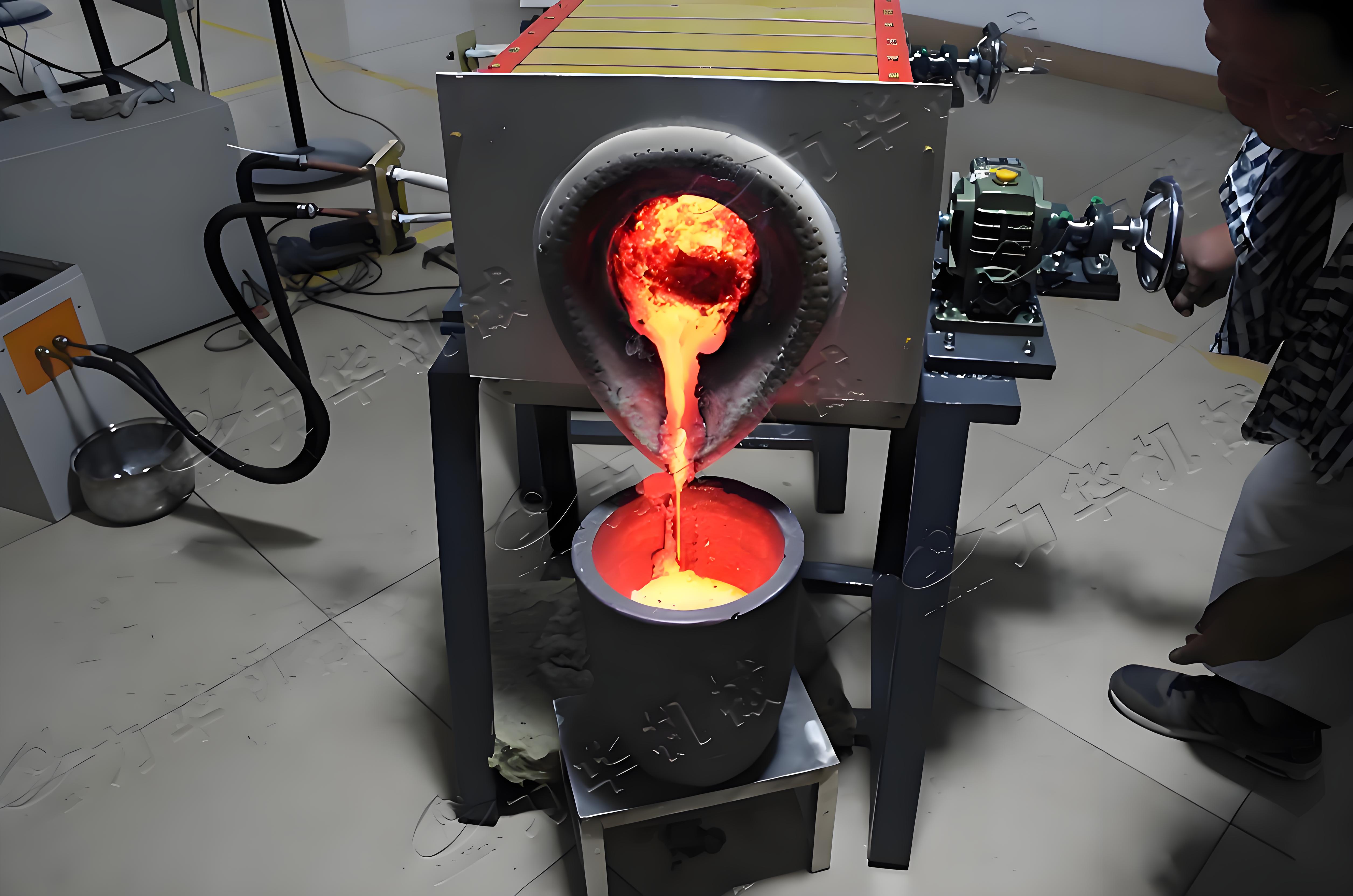
电阻丝加热铝合金熔炉时,铝合金的温度是如何均匀分布的?
- 环形 / 螺旋形缠绕:将电阻丝均匀缠绕在熔炉内壁或底部(如圆柱形熔炉的圆周方向),使热量从四周对称辐射,避免局部过热。
- 分层分区布置:根据熔炉高度或体积,将电阻丝分为若干加热区(如底部、侧壁中部、顶部),通过独立控制各区域功率,补偿不同位置的热损失(如顶部散热较快,可适当增加功率)。
- 辐射反射结构:在电阻丝外侧加装耐高温反射板(如氧化铝或碳化硅材质),将辐射热反射至铝合金表面,减少热量向炉壁的散失,增强中心区域的热辐射均匀性。
- 分段升温控制:初始阶段以高功率快速升温,接近目标温度时降低功率,通过 PID(比例 - 积分 - 微分)控制系统微调,避免温度过冲导致局部过热。
- 多区温度反馈:在熔炉不同位置(如中心、边缘、底部)布置热电偶,实时监测温度并反馈至加热系统,自动调节各区域电阻丝的功率,平衡温度差异。
- 铝合金的导热特性:铝合金本身导热系数高(约 200 W/(m・K)),但固态时热传导效率低于液态。当铝合金熔化后,液态金属的自然对流(因温度差导致密度变化,热液上升、冷液下沉)可加速热量扩散。
- 强制对流强化:通过机械搅拌(如石墨搅拌桨)或电磁搅拌(利用交变磁场驱动液态金属流动),强制液态铝合金循环,打破局部温度分层,使热量均匀混合。例如,电磁搅拌可在不接触金属的情况下产生涡流,避免搅拌装置对金属的污染。
- 电阻丝与铝合金表面的距离保持一致,避免因距离差异导致辐射热强度不同(辐射热强度与距离平方成反比)。例如,在圆柱形熔炉中,电阻丝与炉壁的距离相等,确保圆周方向辐射均匀。
- 炉壁采用低发射率材料(如镀铝涂层),减少炉壁对辐射热的吸收,使更多热量直接作用于铝合金。
- 对称型结构:采用圆柱形或球形炉体,利用几何对称性减少热传递路径的差异,相比方形炉体更易实现温度均匀性。
- 多层保温结构:炉壁由内至外依次为耐高温耐火层(如刚玉砖)、保温隔热层(如陶瓷纤维毯)和金属外壳,减少热量向外界散失,维持炉内温度稳定,避免因炉壁散热导致边缘温度低于中心。
- 在炉内设置导流板或气流通道,引导加热过程中产生的热空气或保护气体(如氮气)均匀流动,通过对流传热辅助铝合金升温。
- 对于大型熔炉,可在顶部设置热风循环系统,将顶部高温气体吹向底部,补偿底部热损失,平衡上下温差。
- 避免升温过快导致热应力集中:低温阶段(如<300℃)采用低功率缓慢升温,减少固态铝合金的热膨胀差异;高温阶段(熔化后)适当提高功率,但需配合搅拌确保液态金属温度同步上升。
- 熔化后延长保温时间:液态铝合金在保温阶段通过自然对流和搅拌进一步均匀温度,通常保温时间根据熔炉体积确定(如每 100 kg 金属保温 30~60 分钟)。
- 多点测温网络:在熔炉内布置 3~5 个测温点(如中心、距壁面 10% 半径处、底部中心),通过 PLC(可编程逻辑控制器)实时采集数据,若温差超过设定阈值(如 ±5℃),自动调整对应区域电阻丝功率。
- 红外测温辅助:利用红外热像仪扫描铝合金表面温度分布,直观识别高温或低温区域,辅助优化电阻丝布局或搅拌策略。
- 小型实验室熔炉:采用螺旋形电阻丝缠绕炉壁,配合底部磁力搅拌,温度均匀性可达 ±3℃以内,适用于精密合金熔炼。
- 大型工业熔炉:通过分区电阻丝加热(如底部 2 区、侧壁 4 区)+ 电磁搅拌 + 热风循环,可使 10 吨以上铝合金熔体的温差控制在 ±10℃,满足压铸或铸造的温度要求。
影响维度 | 关键措施 |
---|
电阻丝布局 | 环形缠绕、分区控温、反射板增强辐射均匀性 |
热传递机制 | 利用液态金属自然对流 + 强制搅拌(机械 / 电磁),强化热传导与对流 |
熔炉结构设计 | 对称型炉体、多层保温层、导流板引导气流 |
过程控制 | 分段升温、多点测温反馈、PID 功率调节 |
通过上述设计,电阻丝加热铝合金熔炉可实现温度的高效均匀分布,确保铝合金熔炼质量的稳定性。
文章源自炬鼎熔炉-江浙沪铝合金集中熔化炉厂家|中频感应熔炼炉|铝屑熔解炉报价-品牌直供·节能技术-https://www.judrl.com/3762.html文章源自炬鼎熔炉-江浙沪铝合金集中熔化炉厂家|中频感应熔炼炉|铝屑熔解炉报价-品牌直供·节能技术-https://www.judrl.com/3762.html
来自外部的引用